The manufacturing sector has witnessed an increase in the incorporation of robotics in its production processes. This has come about as a result of the rapid technological advancements in robotics and automation.
Tasks with high precision and repeatability are being performed by industrial robots resulting in higher quality products. Manufacturers are noting an increase in output, due to industrial robots’ ability to work continuously without taking breaks.
Additionally, the robots’ ability to work in hazardous and harmful settings has greatly improved the working conditions and security of the production plants.
There are six industrial robots, based on their mechanical configuration, that are used in manufacturing processes. In this article, we are going to look at the four major types of robots, together with their advantages and disadvantages.
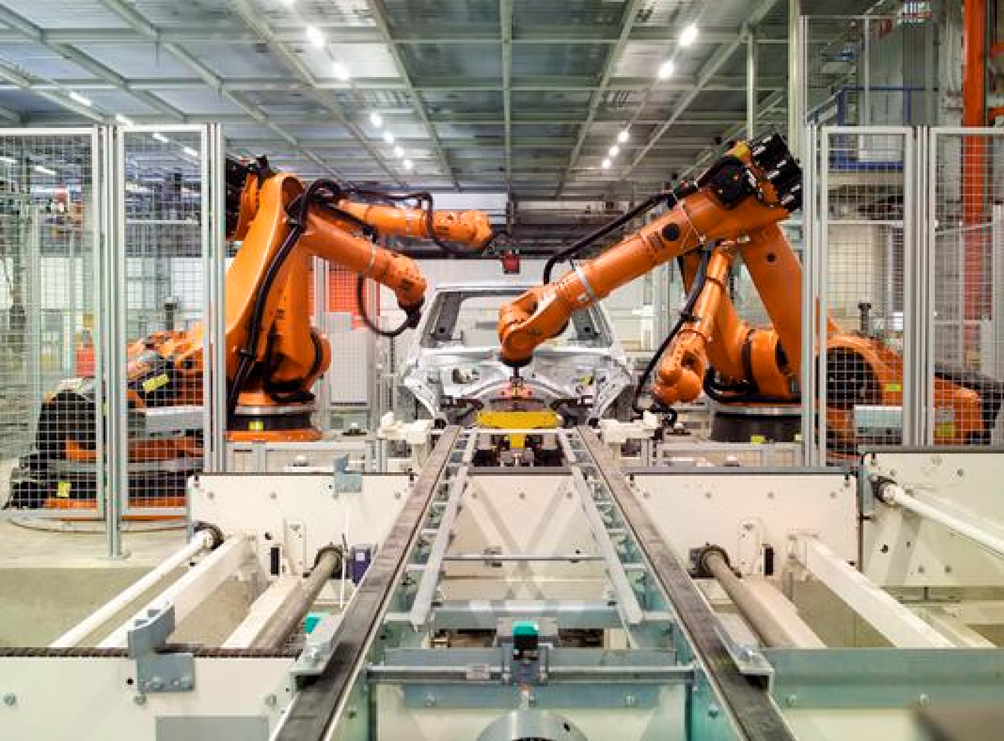
Articulated Robots
This is one of the most common types of industrial robots. In its mechanical configuration, the articulated robot resembles a human arm. The arm is usually connected to the base via a twisting joint.
Articulated robots usually have two to ten joints, which provide an added degree of freedom. Articulated robots that have six degrees of independence are the most frequently used industrial robots, as their design offers maximum flexibility.
Articulated robots can be used for food packaging, machine tending, glass handling, spot welding, and steel bridge manufacturing.
Advantages of Articulated robots
- More comfortable to align with various planes
- High speed
- Big work cover for minimum floor space
Disadvantages of Articulated robots
- Complex kinematics
- Requires a keen robot supervisor
- Intricate programming
Cartesian Robots
Also known as gantry or rectilinear robots, cartesian robots usually have a rectangular configuration. These types of industrial robots usually have three prismatic joints that help them slide on their X, Y, Z perpendicular axes to deliver linear motion.
Cartesian robots are used in various industrial applications such as; pick and place operations, adhesive applications, assembly and sub-assembly, loading and unloading, nuclear material handling, and material handling.
Advantages of Cartesian robots
- Fewer costs
- Easy to program offline
- Extremely customizable
- Simple to operate
- Ability to handle heavy loads
Disadvantages of Cartesian robots
- Their motion is restricted to only one direction at a time
- Requires large installation and operating areas
- Complicated assembly
SCARA Robots
Selective Compliance Assembly Robot Arm (SCARA) robots usually have a donut-shaped work cover. They consist of two parallel joints that offer compliance in a particular plane. The end effector on the SCARA robots are usually attached to the arm, and they move horizontally, while the rotary shafts are generally vertically positioned.
Due to their specialty in lateral movements, SCARA robots are usually used for assembly applications, packaging, machine loading, Biomed applications, palletizing, and semiconductor wafers handling.
Advantages of SCARA robots
- They are excellent for repetitive tasks
- High speed
- Large workplace
Disadvantages of SCARA robots
- They are hard to program offline
- They require a dedicated robot supervisor
- They are restricted to two-dimensional surfaces
Delta Robots
They are also known as parallel link robots as they consist of similarcombinedlinksthat are usually connected at a common base. The positioning of the end effector can be easily controlled since each joint usually has direct control over the end effector resulting in high-speed operations.
Parallel link robots usually have a dome-shaped work cover and are used in various applications, including; flight simulators, optical fiber alignment, pharmaceutical industry, automotive simulators, and electronic industry.
Advantages of Delta robots
- Their operational accuracy is usually very high
- They operate at very high speeds
Disadvantages of Delta robots
- They require a devoted robot supervisor
- Their operation is complicated
Conclusion
Before incorporating automated industrial robots in your business, it is good to know about the different types of robotics in the market in order to select an appropriate type for your operations.
Apart from the four types of robotics discussed in this article, we have two more, namely: cylindrical robots and polar robots. For you to make the best decision on the kind of robot to implement in your operations, some factors such as; speed, accuracy, positioning, weight, duty cycle, portability, and setting must be considered.